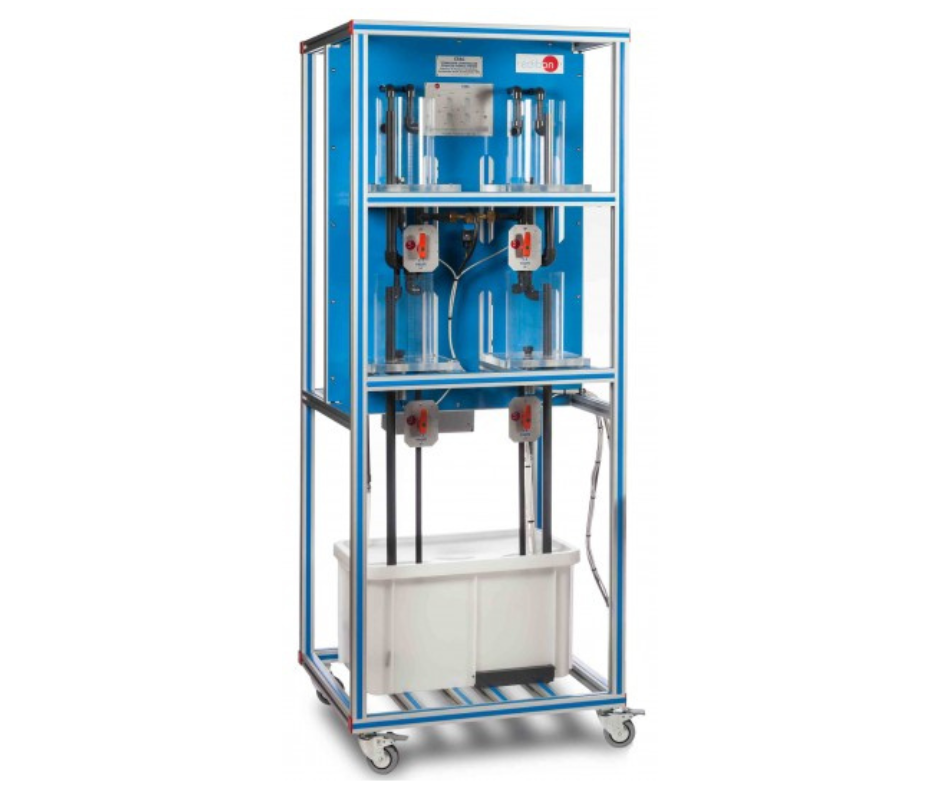
COMPUTER CONTROLLED COUPLED TANKS SYSTEM
ชุดศึกษาการควบคุมระดับของเหลว
INTRODUCTION
Nowadays, several industrial applications require liquid level control as part of more complex processes, e.g., in food processing, beverage, dairy, etc. Many times these processes require the liquids to be pumped, stored in tanks and then driven to other tanks, obtaining a coupled tank system.
Since the levels of the coupled tanks interact between each other, level and flow control is required to maintain a constant level of the liquid in the tanks.
The Computer Controlled Coupled Tanks System, “CTAC”, is a four interconnected tanks system designed by EDIBON that includes the typical actuators used in liquid level control systems, such as pumps and valves, used to pump the liquid between tanks. In addition, there are pressure sensors that provide liquid level measurement for feedback control. The unit is supplied with a set of practical exercises that introduce the student into the control design methodology for a coupled tanks system.
EXERCISES AND PRACTICAL POSSIBILITIES TO BE DONE WITH THE MAIN ITEMS
- Study of nonlinear systems.
- Determination of the linear model of a tank: linearization.
- Determination of the linear model of a system with two coupled tanks.
- Study of the structure of a PID controller.
- PID control of the water level in a tank.
- Simultaneous control of the water level in a system formed by two tanks.
- Identification of systems.
- Study of different tanks coupling configurations.
- Study of the influence of some tanks on others in a four tanks system.
- Study of decouplers.
- Disturbance rejection.
Additional practical possibilities: - Sensors calibration.
Other possibilities to be done with this Unit: - Many students view results simultaneously.
To view all results in real time in the classroom by means of a projector or an electronic whiteboard. - Open Control, Multicontrol and Real Time Control.
This unit allows intrinsically and/or extrinsically to change the
span, gains; proportional, integral, derivative parameters; etc, in
real time. - The Computer Control System with SCADA and PID Control allow a real industrial simulation.
- This unit is totally safe as uses mechanical, electrical/electronic, and software safety devices.
- This unit can be used for doing applied research.
- This unit can be used for giving training courses to Industries even to other Technical Education Institutions.
- Control of the CTAC unit process through the control interface box without the computer.
- Visualization of all the sensors values used in the CTAC unit process.
– By using PLC-PI additional 19 more exercises can be done.
– Several other exercises can be done and designed by the user.